نتایج جست و جو برای: بازرسی چشمی جوش
دپارتمان آموزش گروه مهندسین مشاور و بازرسی فنی بهینه کاوش صنعت (BKS)
دپارتمان آموزش گروه مهندسین مشاور و بازرسی فنی بهینه کاوش صنعت (BKS)
دپارتمان آموزش گروه مهندسین مشاور و بازرسی فنی بهینه کاوش صنعت (BKS)
شرکت مدیریت مهندسی و بازرسی فنی گاماراد
دوره آموزشی بازرسی چشمی جوش و CWI
دوره آموزشی بازرسی چشمی و CWI
دوره آموزشی بازرسی چشمی و CWI
تاریخ شروع : شنبه ۲۵/دی/۱۳۹۵
مدت دوره :۵ روز
تقویم آموزشی دوره های بازرسی جوش بهمن ۹۵
مدرسین دوره : کارشناسان سطح ASNT III و ISO 9712
دانلود تقویم آموزشی دوره های بازرسی جوش نیمسال دوم ۱۳۹۵ شرکت گاماراد
به دلیل محدود بودن ظرفیت دوره های آموزشی فوق اولویت با ثبت نام کنندگان قطعی می باشد.
شرکت مدیریت مهندسی و بازرسی فنی گاماراد
شرکت مدیریت مهندسی و بازرسی فنی گاماراد
دوره آموزشی بازرسی چشمی و CWI
تاریخ شروع :یک شنبه ۲۸/آذر/۱۳۹۵
مدت دوره :۵روز
دوره آموزشی بازرسی التراسونیک UT
تاریخ شروع :پنج شنبه ۰۹/دی/۱۳۹۵
مدت دوره :۸ روز ویژه پنج شنبه و جمعه ها
دانلود تقویم آموزشی دوره های بازرسی جوش نیمسال دوم ۱۳۹۵ شرکت گاماراد
Phone + 98 21 ۴۴۲ ۹۸۱ ۷۴
Mobile + 98 91 ۰۱۳ ۰۶۷ ۳۷
Fax + ۹۸ ۲۱ ۴۴۲ ۹۸۱ ۷۵
شرکت مدیریت مهندسی و بازرسی فنی گاماراد
شرکت مدیریت مهندسی و بازرسی فنی گاماراد
دوره آموزشی بازرسی چشمی و CWI
شروع دوره ۰۶آبان ۹۵ویژه پنج شنبه و جمعه ها
دوره آموزشی بازرسی مایعات نافذ و ذرات مغناطیسی PT , MT
شروع دوره ۰۸ آبان ۹۵
دوره آموزشی بازرسی التراسونیک شروع دوره ۲۲ آبان ۹۵
دانلود تقویم آموزشی دوره های بازرسی جوش نیمسال دوم ۱۳۹۵ شرکت گاماراد
Phone + 98 21 ۴۴۲ ۹۸۱ ۷۴
Mobile + 98 91 ۰۱۳ ۰۶۷ ۳۷
Fax + ۹۸ ۲۱ ۴۴۲ ۹۸۱ ۷۵
ایستا صنعت جوش
شرکت مهندسین مشاور و بازرسی فنی
ایستا صنعت جوش
یکی از پرشتاب ترین سازمانهای ارائه دهنده خدمات بازرسی فنی و مهندسی جوش در کشور
آدرس : کرج – میدان مادر – خیابان درختی – پلاک ۳۴۶ – ساختمان اشکان – طبقه ۳ – واحد۱۱
دوره آموزشی بازرسی جوش (CWI)
شرکت فنی و مهندسی نفتا کیفیت آزما
دوره آموزشی بازرسی چشمی جوش VT
بازرسی جوش CWI
جمعه و پنجشنبه ها
مراجعه به سایت
www.weld-eng.ir
۰۲۱۸۹۷۷۳۸۳۳-۰۹۳۸۲۵۵۷۱۵۴
بازرسی جوش ساختمان وسازه(جلسه سوم)
|
بازرسی جوش ساختمان و سازه (جلسه دوم)
بازرسی قبل از جوشکاری
A. اطلاع از کیفیت مورد نظر کار و میزان حساسیت سازه
:بطور قطع یک بازرس در شروع کار جوشکاری یک سازه فلزی بایستی از موقعیت سازه آگاهی کافی داشته باشد و موارد ذیل را مورد بررسی قرار
داده باشد :آیا محل استقرار سازه در منطقه زلزله خیز قرار گرفته است ؟آیا محل استقرار سازه در منطقه ای است که در معرض خوردگی اتمسفری یا
خوردگی شیمیایی است ؟آیا محل استقرار سازه در منطقه سردسیر است یا گرمسیر ؟بار گذاری سازه بر اساس استاتیکی محاسبه شده یا دینامیکی ؟تعداد
طبقات اسکلت فلزی ، نحوه اتصالات ، ضخامت ورق ها ، موقعیت و تجهیزات کارگاهی نیز از مواردی است که بایستی مورد بررسی قرار گیرند .
B. مطالعه دقیق نقشه ها و مشخصات فنی (اجزاء جوش ، اندازه ها و مشخصه فرآیند ) :
معمولاً مهندسین سازه ، ابعاد مقدار جوش را در نقشه ها مشخص می کنند و با علائم محل جوش و اتصالات را نشان می دهند . لذا مطالعه دقیق نقشه ها
علاوه بر اطلاع یافتن از موارد فوق ، جهت برنامه ریزی برای ارائه یک الگوی بازرسی در مراحل مختلف پروژه مهم و ضروری است .
C. مقایسه مشخصه داده شده توسط مشتری و کیفیت مورد نیاز با محصول .
D. مطالعه استانداردهای مربوطه و انتخاب استانداردهای اجرایی :
مروری بر استانداردهای جوش در سازه های فلزی به عنوان مرجع نهایی بازرسی و کنترل کیفیت جوش امری ضروری است . در بعضی موارد می
توان بر اساس استانداردهای بین المللی برداشتهایی متناسب با کار از استاندارد اقتباس و در اجرا بکار گیرد .البته هر نوع برداشتی کارشناسانه از
استاندارد که منطبق با استاندارد نباشد ، قبل از اجرا بایستی در نمونه های تست تایید شده باشد (PQR) .
E: انتخاب و ارزیابی روش جوشکاری:ب
طور کلی در اسکلت های فلزی عمدتاً از روش های الکترود دستی و جوشکاری زیر پودری و در مواردی از جوشکاری با گاز محافظ استفاده می شود .
در موقع نصب سازه فلزی از روش الکترود دستی استفاده می شود، اما در موقع اتصال ورق ها به هم دیگر و ساخت ستون و نیز تیر ورق در مواردی که
جوشکاری بصورت طولی و سری می باشند برای بالا بردن سرعت کار ، کیفیت ظاهری بهتر و نفوذ بیشتر میتوان از روش جوشکاری زیر پودری تنها
می توان در حالت تخت و افقی جوشکاری نمود و در حالت سربالا ، بالای سر و سرازیر جوشکاری امکان پذیر نیست .
F
. انتخاب مصالح و بازرسی مصالح:
منظور از مصالح عمدتاً شامل صفحه سنگ ساب ، برس سیمی ، انبر جوشکاری ، ماسک و شیشه ماسک جوشکاری می باشد ، که انتخاب صحیح و
بازرسی آنها از نظر کیفیتی و نیز موارد ایمنی در موقع جوشکاری اسکلت فلزی موثر و مفید است .
G
. انتخاب مواد مصرفی و بازرسی مواد مصرفی:
نحوه انتخاب مواد مصرفی جوشکاری ، بازرسی و تست آنها باید بر اساس معیار استانداردها و دستورالعملها انجام گیرد زیرا اطمینان از سالم بودن و
مرغوبیت مواد مصرفی در دستیابی به کیفیت بالا در اتصالات جوش نقش تعیین کننده دارد .
G
I. در انتخاب الکترود دو مطلب باید در نظر گرفته شود :
۱) نوع الکترود
۲) سایز الکترود
در خصوص انتخاب نوع الکترود باید موارد ذیل را در نظر گرفت :
ترکیب شیمیایی فلز پایه
نوع تنش و مقدار تنش
درجه حرارت سرویس
خوردگی محیط
نوع جریان الکتریکی ، قطبیت و وضعیت جوشکاری
نرخ رسوب
سهولت کار
قیمت الکترود
در خصوص سایز الکترود باید به موارد زیر توجه کرد :
ضخامت قطعه
طرح اتصال
وضعیت جوشکاری
سهولت کار
کیفیت جوش
هزینه
بازرسی مواد مصرفی جوش توسط بازرس می تواند به دو صورت انجام گیرد :
انجام آزمایش بر روی خواص جوش الکترود و یا پودر و مفتول مصرفی جوش
اخذ گواهی از شرکت های معتبر سازنده الکترود ، پودر یا مفتول جوشکاری
G2. بازرسی ورق های مصرفی :
ورق های مصرفی بایستی از نظر ترکیب شیمیایی و خواص مکانیکی کنترل شوند ، چون اغلب دیده شده است که ورق های خریداری شده بعضاً مطابق با کد فولاد خواص مکانیکی آن مطابق نیست . لذا بایستی به منظور بررسی خواص مکانیکی ورق در جهت نورد و خلاف جهت نورد نمونه برداری انجام داده و آزمایش کشش جهت بررسی استحکام فولاد صورت گیرد . ضمناً علاوه بر تست عدم تورق از نظر ظاهری ورق ها باید کنترل و بازرسی شوند ، بعضاً سطوح ورق ها دارای ترک ، ناپیوستگی های زیاد ، زنگ زدگی شدید و در مواردی از نظر ابعاد دو پهن می باشند .
در صورت مشاهده ترک های ناشی از تورق و یا ناپیوستگی های سطحی می توان مطابق جدول زیر به تعمیر و عملیات اصلاحی اقدام نمود .(AWS D1.1 Sec5)
محدوده پذیرش و یا تعمیر ناپیوستگی های تورقی ناشی از نورد در سطح برش خورده
شرح ناپیوستگی تعمیر لازم
هر نوع ناپیوستگی با طول مساوی ۲۵ میلیمتر لازم نیست
هر نوع ناپیوستگی با طول بزرگتر از ۲۵ میلیمتر و عمق کمتر از ۳ میلیمتر لازم نیست ولی عمق باید مورد بررسی قرار گیرد
هر نوع نایوستگی با طول بزرگتر از ۲۵۵ میلیمتر و عمق ۳ تا ۶ میلیمتر باید کاملاً برداشته ولی جوش لازم نیست
هر نوع ناپیوستگی با طول بزرگتر از ۲۵ میلیمتر و عمق بیش از ۶ میلیمتر باید کاملاً برداشته و با جوش پر شود
در مواردی که سطح ورق ها دارای ناپیوستگی های عمیق و یا حفره دار باشند و در شرایطی که استاندارد اجازه داده باشد می توان توسط عملیات جوشکاری آنها را ترمیم کرد ، این کار بهتر است اولاً با الکترودهای کم هیدروژن مانند E7018 اصلاح شوند ، و پس از جوشکاری با آزمایش های MT یا PT از کیفیت کامل موضع جوشکاری شده اطمینان حاصل نمود.
H. بازرسی وسایل و تجهیزات جوشکاری ، برشکاری و عملیات حرارتی.
I. طرح و تنظیم و یا ارائه دستورالعمل جوشکاری :
یک بازرس می تواند دستورالعمل جوشکاری (WPS) مربوط به سازه فلزی مورد نظر را تدوین و تهیه کند یا اینکه دستورالعمل جوشکاری توسط یک مهندس جوش تدوین و تایید شده باشد و بازرس با در دست داشتن دستورالعمل مربوطه تمامی بندهای دستورالعمل را در ابتدای شروع کار به اپراتور و کارشناسان پروژه توضیح داده و سپس مطابق آن کنترل های لازم را اعمال نماید .دستورالعمل جوشکاری معمولاً باید توسط تست و آزمایشاتی که در استاندارد به آن ارجاع داده شده بوسیله آزمایشگاه معتبر تایید گردد که به اصطلاح PQR آن گردد .موارد مهمی که در دستورالعمل جوشکاری (WPS) بایستی به آن اشاره شود عبارتند از :نوع فرایند جوشکاری ، نوع ضخامت ورق مصرفی ، نوع و قطر الکترود مصرفی ، مشخصات الکتریکی دستگاه جوش و اتصال الکترود ، ترتیب جوشکاری ، نحوه تکنیک جوشکاری ، عملیات حرارتی پیش گرم و یا پس گرم کردن .تست هایی که در گزارش کیفیت دستورالعمل جوش (PQR) بکار برده می شوند و معمولاً در استانداردنیز به آنها توجه شده است شامل :
بازرسی چشمی
آزمایشات غیر مخرب ، PT یا MT و UT یا RT
آزمایش کشش عرضی
آزمایش خمش
آزمایش ضربه در شرایط خاص یا به تشخیص بازرس
J .آزمون جوشکاران و اپراتورها و بررسی صلاحیت آنها:
تمامی جوشکاران بایستی قبل از جوشکاری بر روی سازه فلزی توسط بازرس تعیین صلاحیت شوند . بازرس بایستی متناسب با نوع نیاز و روش و الکترود و نحوه اتصالات جوش در سازه از جوشکاران بر اساس استاندارد آزمایش بعمل آورد و پس از تایید ، متناسب با نوع تایید و گواهی که هر جوشکار دریافت می کند بایستی در پروژه از وی استفاده شود . جوشکارانی که کیفیت جوش آنها تایید نشده است نمی توانند جوشکاری نمایند . معمولاً در صورت تست در حالت گوشه علاوه بر کنترل چشمی ظاهر جوش ، آزمایش شکست نمونه جوش گوشه انجام می شود و در صورت جوشکاری در حالت نفوذی و اتصال لب به لب علاوه بر کنترل چشمی آزمایش خمش و یا آزمایش غیر مخرب UT با RT انجام می شود .
J. بررسی تسهیلات آزمایش بازرسی در حین جوشکاری
A. بازرسی قطعات مونتاژ شده و درزهای جوشکاری:ن
حوه اتصال جوش از نظر زوایای پخ سازی ، فاصله ریشه اتصال ، فاصله پیشانی اتصال بایستی کنترل شود . همچنین نحوه اتصالات گوشه محل استقرار اتصال سپری از نظر یکنواختی فواصل در طول اتصال بایستی کنترل شود . (بر اساس WPS )
B. بازرسی محل های جوش و سطوح مجاور جوش به منظور اطمینان از تمیزی و عدم آلودگی با موادی که اثرات زیان بخشی بر جوش دارند:
معمولاً سطوح پخ سازی شده چون با هوا برش انجام می شود ، ممکن است پوسته های اکسیدی داشته باشد که حتماً بایستی تمیز و عاری از اکسیدهای سطحی باشد ، همچنین چربی ، گریس ، روغن و زنگ زدگی و رنگ روی سطوح اتصال بایستی کاملاً تمیز شوند زیرا در غیر این صورت باعث بروز عیوب سطحی و داخلی در جوش خواهند شد .
C. بازرسی سطوح جوشکاری شده با شعله یا شیار زده ، از نظر پوسته ، ترک و غیره.
D. بازرسی و ترتیب و توالی جوشکاری ، استفاده از قیدها ، گیره ها و سایر تمهیدات به منظور کنترل پیچیدگی ناشی از جوشکاری :
رعایت ترتیب جوشکاری باعث پیشگیری از پیچیدگی در جوش و ورق و نیز باعث جلوگیری از بروز عیوبی از جمله ترک ، عدم نفوذ ، عدم ذوب و غیره می شود .در صورت عدم رعایت ترتیب جوشکاری تنش های پسماند در اتصال جوش افزایش پیدا خواهد کرد. تنش های پسماند تنش هایی هستند که در قطعه می مانند ، حتی اگر بار خارجی بر روی قطعه وجود نداشته باشد. (بر اساس WPS ).
E. بازرسی مواد مصرفی جوشکاری از نظر مقدار رطوبت در روپوش الکترودهای قلیایی و یا پودرهای جوشکاری طبق دستورالعمل های ارائه شده در استانداردها:
الکترودهای جوشکاری بایستی از آلوده شدن به رطوبت و روغن مصون بمانند . همچنین الکترودها را در هنگام جوشکاری نباید خم کرد ، این کار باعث شکستن روکش الکترود و ایجاد عیوب در فلز جوش هنگام جوشکاری می شود .شرایط انبار داری بایستی به صورتی باشد که اولاً رطوبت نسبی هوای انبار حداکثر ۶۰ درصد و درجه حرارت انبار بیش از ۱۸ درجه سانتیگراد باشد . ضمناً قفسه ها و طبقات نگهداری الکترود بایستی نسبت به دیوار و کف انبار فاصله داشته باشد و هنگام حمل ضربه نخورد . در زیر جدولی در رابطه با شرایط الکترودهای قلیایی آورده شده است .(شرایط مجاز جهت نگهداری و خشک کردن الکترودها )مقادیر مجاز تماس الکترودهای کم هیدروژن با هوای آزاد
F. بازرسی جوشکارنی که تایید صلاحیت شده اند:بازرس مجاز می باشد چنانچه جوشکار قبلاً در تست اولیه صلاحیت وی تایید شده باشد ولی در حین کار اصول کیفیتی را رعایت نکند یا کیفیت جوشکاری او مورد تایید نباشد از ادامه کار آن جلوگیری بعمل آورد .معمولاً جوشکاری که تایید صلاحیت شده است ، اگر بیش از ۶ ماه در حالت پذیرفته شده جوشکاری نکند بایستی مجدد از وی تست صلاحیت گرفته شود.
برگرفته از سایت شرکت آرون جوش صنعت
کاربر گرامی ادامه مقاله را درجلسات آینده بخوانید.
مهندسین مشاور ناظران دقیق تدبیر برگزار می کند:
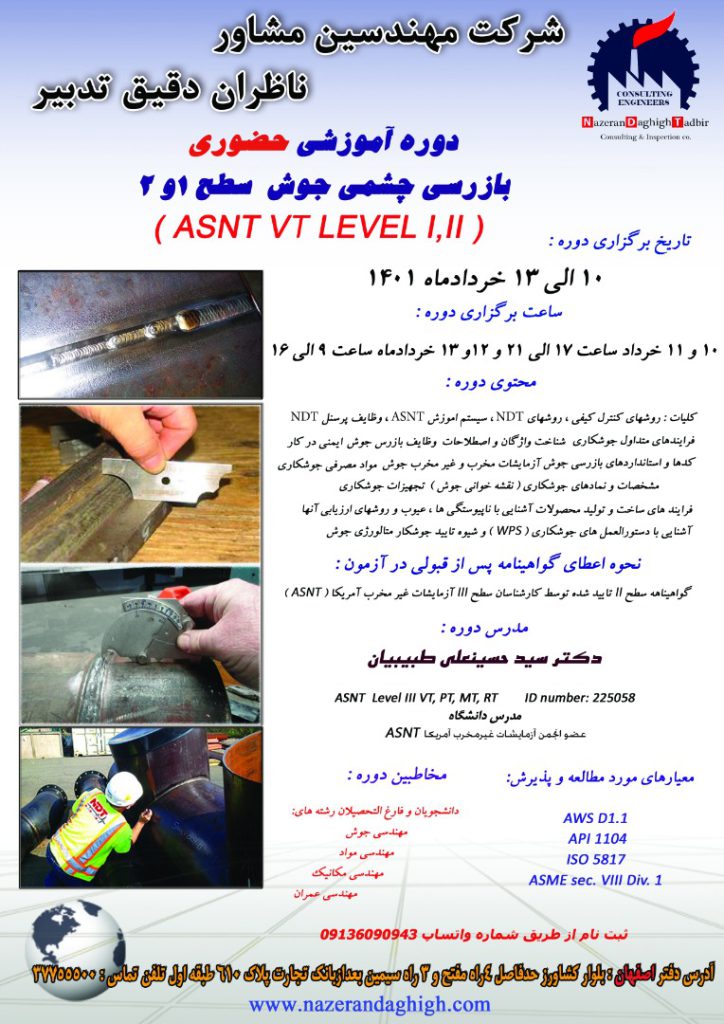
دوره ی آموزش حضوری بازرسی چشمی جوش سطح ۱ و ۲ (ASNT VT LEVEL I & II)
تاریخ برگزاری: ۱۰ الی ۱۳ خرداد ماه ۱۴۰۱
جهت ثبت نام با شماره ی ۰۹۱۳۶۰۹۰۹۴۳ در واتساپ تماس حاصل فرمایید.
مهندسین مشاور ناظران دقیق تدبیر برگزار می کند:
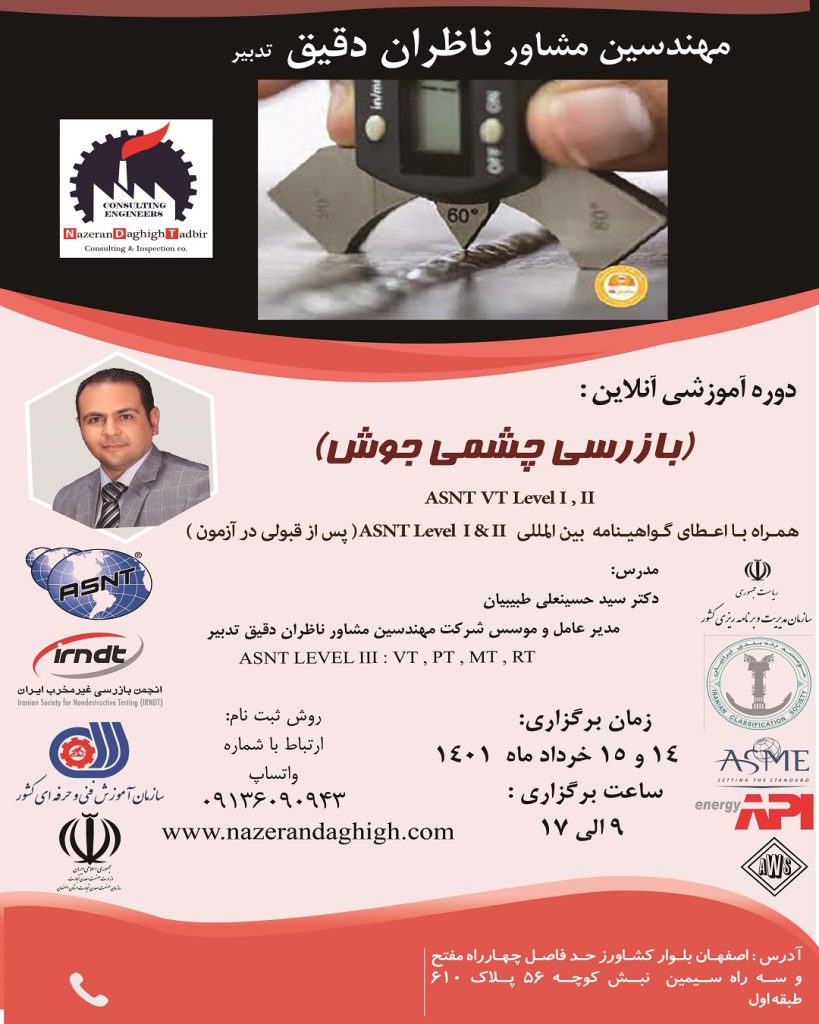
دوره ی آموزشی آنلاین بازرسی چشمی جوش
همراه با اعطای گواهینامه بین المللی ASNT Level I & II
جهت ثبت نام با شماره ی ۰۹۱۳۶۰۹۰۹۴۳ در واتساپ تماس حاصل فرمایید.